Flex Circuits
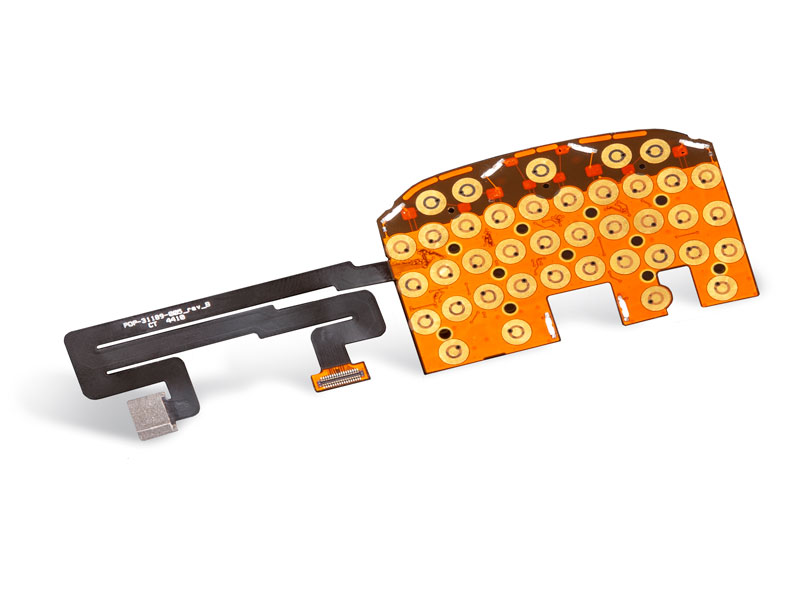
FPC Basics
Flexible printed circuits, also called flex circuits or FPCs, are assembled by mounting a conductive layer onto a flexible substrate such as polyimide. The unique mechanical properties of polyimide and ductility of copper foil allow the FPC to flex and bend without becoming damaged. Because of these inherent rigorous characteristics, FPCs can withstand harsh operating environments, adding to their design versatility.
As an innovative electronics manufacturer, SSI produces high-performance custom flexible printed circuits designed for optimal performance and enhanced reliability and durability.
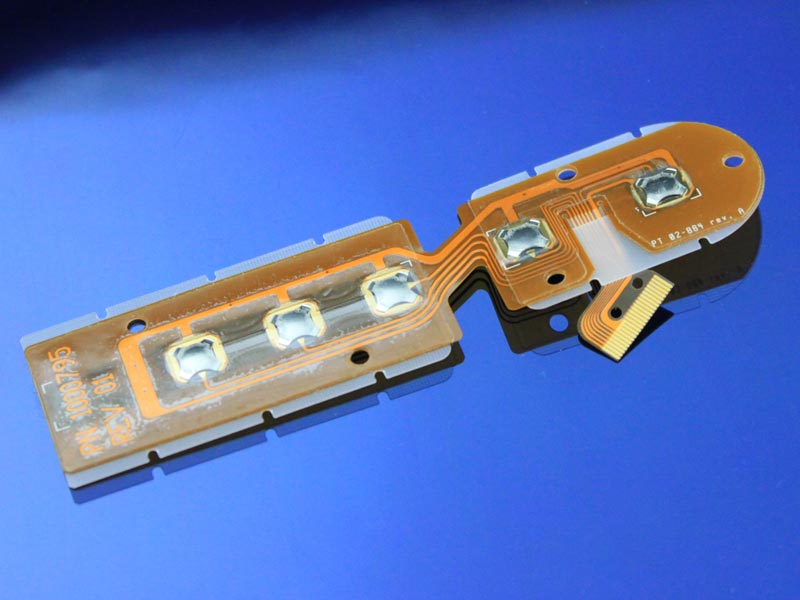
Flex Circuit Design Versatility
Combining the processing capabilities of rigid-PCBs with the ability to conform to unique geometries, SSI Electronics’ flexible printed circuits (FPCs) provide a unique medium for electrical circuits. These versatile circuits are produced by etching copper-cladded polyimide film, which provides a platform for a wide variety of secondary processing. Contact SSI for the flexible circuits your application requires or view our flexible circuit design guide for additional information about design features, interface options, and more. Or call 800-866-8510 today!
FPC Application Uses
Flex circuits allow for extreme design flexibility making them excellent for both simple and complex applications. FPCs are used throughout various technology and electronics-based industries and applications, including:
- Aerospace/Aviation
- Automotive
- Battery Packs
- Cell Phones
- Fuel Pumps
- Heart Monitors
- Military
- Satellites
What Do You Mean “Flexible Printed Circuits Aren’t Printed”?
It’s no wonder that circuit terminology can be so confusing. As the most common circuits in the world, printed circuit boards (PCBs), are not, in fact, printed…they’re etched! The same goes for flexible printed circuits (FPCs). In addition to the frequent confusion associated with the term “printed,” it is also common for people to misunderstand the difference between printed circuit boards and flexible circuits.
Designers and engineers often place PCB and FPC in similar categories and assume that flex circuits are simply printed circuits boards that can be bent and folded, but the two are different. Yes, they both perform the same electrical function and have similar construction, but they are manufactured using different types of materials.
4 Key Advantages of Custom Flex Circuits for Electronics
Flexible circuits provide an incredible amount of design versatility because they are lightweight, bendable, foldable, and can be configured to match a range of size and space requirements. The four key advantages of using flexible circuits for electronics include:
Compared to standard printed circuit boards (≈0.063” thick), flex circuits provide a dramatic decrease in package size and weight. Flex circuits, typically just 0.004”-0.010” thick, are even thinner and lighter than traditional cable options.
Interconnect problems can often be solved by flex circuits, which integrate the interconnects into the part. Thus, flexible circuits eliminate the need for expensive cables and connectors.
With the interconnections built into the flex circuit, fewer connectors are required, and thus less soldering. The ability to pre-form the flex circuit assembly, along with its inherent flexibility, allows quicker installation, particularly in hard-to-reach areas.
Certain applications require circuits that can flex. Compared to other flexible options, flex circuits provide superior electrical and mechanical performance.
Common Types of Flex Circuits
To help clear things up, below you will find brief descriptions of the most common types of circuits:
Copper-cladded film (usually polyimide) that is chemically etched to produce a specific circuit pattern. Rolled Annealed copper is used for flex circuits because it is more flexible than the Electro Deposited copper used for printed circuits. Also, the adhesive used for FPCs must have the right chemical and thermal properties as well as the ability to maintain its flexibility after the adhesive dries.
Copper-cladded, fiberglass-reinforced (rigid) laminate that is chemically etched to produce a specific circuit pattern. Printed circuit boards, or PCB’s do not need to flex, so Electro Deposited copper and standard adhesives are sufficient materials. The board is typically made of an epoxy resin reinforced with glass fibers or papers.
Conductive polymer ink, usually silver, screen printed on thin film, typically polyester, to create a specific circuit pattern. This type of circuit is typically installed on a flat surface that does not bend or flex.
Thin copper conductors that are laminated between two layers of polyester insulators to create a cable. These are similar to flex circuits in that they can repeatedly fold and bend without damaging the circuits.